Keystone Tower System is ready to launch its spiral welded towers to the wind industry
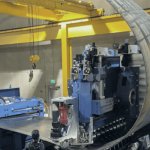
[ad_1]
Keystone Tower Systems will expand its presence in the wind industry with its patented spiral welded steel towers.
Keystone’s tapered spiral welding technology can dramatically reduce the cost and time of building towers on land and at sea, adding strength and saving steel compared to traditional box-welded towers. Its towers will allow turbines to reach higher heights for stronger winds while solving transportation constraints and opening up new regions to wind power.
“Scaling up automated spiral welding to taller towers will support the next phase of cost reduction and growth for the wind industry as we address the need to drive the electricity sector to higher levels. net zero goals, â€said Steve Lockard, Chairman of the Board of Keystone.
Denver-based Keystone holds more than 100 patents in 30 countries born out of research co-founders Eric Smith and Rosalind Takata began after meeting at MIT. In search of innovations that could significantly increase the profitability of wind power, they developed a way to adapt spiral welding technology already proven in the pipe industry to the wind industry.
“Spiral welding enables a new level of automation, resulting in faster production and higher quality,†Smith said. “The result is a tower that can be built 10 times faster than conventional towers, cost-effectively reach heights of 160 meters and beyond, and can still be installed with existing cranes and an identical interface with the hubs of the tower. turbine. “
A successful small-scale demonstration project has been underway since 2015. In 2019, the company secured Series B funding and is close to completing its first large-scale plant in Pampa, Texas. By 2023, the company plans to offer the ability to manufacture cost-effective towers on-site for wind farms across the country.
Keystone received up to $ 5 million from the U.S. Department of Energy in 2019 to develop mobile manufacturing equipment that can manufacture spiral wind towers at the site of onshore wind farms. This avoids the transportation constraints that limit canister welded pylons to sizes that can be moved on a highway.
A single machine will use the steel shipped flat to the site to complete assembly, rolling, fitting, welding and separation for the continuous production of tapered steel tower shells. These on-site manufacturing facilities can be deployed in the short term and produce one megawatt-scale tower per day.
Keystone’s technology unlocks the potential of taller towers to which the National Renewable Energy Laboratory has devoted years of research, culminating in the May 2019 report, “Raising the Height of Wind Turbines: Opportunities and Challengesâ€.
Keystone News
Filed under: News
[ad_2]